Chrome plated steel tubes are coated with a layer of metal on the surface of the steel pipe metal through electroplating. The most important purpose of chromium plated steel pipes is protection. Chromium plated steel pipes have good chemical stability and do not react in alkali, sulfides, nitric acid, and most organic acids. Chromium plated steel pipes can dissolve in hydrochloride acid (such as hydrochloride acid) and hot sulfuric acid. Secondly, chromium plating has good heat resistance, and chromium plated steel pipes only oxidize and discolor when the temperature is greater than 500 degrees Celsius. Moreover, his friction coefficient, especially dry friction coefficient, is the lowest among all metals, and chrome plated steel pipes have excellent wear resistance. In the visible light range, the reflection ability of chromium is about 65%, between silver (88%) and nickel (55%). Chromium does not change color, and chrome plated steel pipes can maintain their reflection ability for a long time when used, which is better than silver and nickel. There are three types of chrome plated processes.
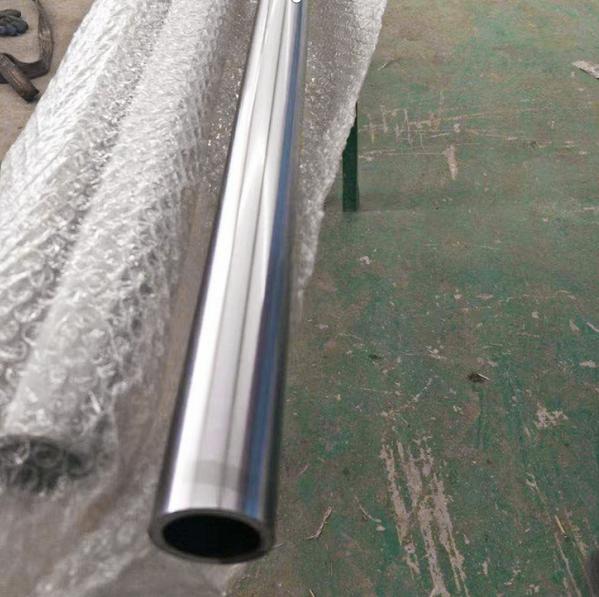
1. Protection - Decorative Chromium Plating Protection - Decorative Chromium Plating, commonly known as Decorative Chromium, has a thin and bright coating that is usually used as the outer layer of multi-layer electroplating. To achieve protection purposes, a sufficiently thick intermediate layer must be first plated on a zinc based or steel substrate, and then a bright intermediate layer of 0.25-0.5 must be plated on top of it μ Thin layer chromium of m. Commonly used processes include Cu/Ni/Cr, Ni/Cu/Ni/Cr, Cu Sn/Cr, etc. After polishing the surface of the product with decorative chromium plating, a silver blue mirror luster can be obtained. Does not change color after prolonged exposure to the atmosphere. This type of coating is widely used for the protection and decoration of components such as automobiles, bicycles, sewing machines, watches, instruments, and daily hardware. The polished decorative chromium layer has a high reflective ability to light and can be used as a reflector. Plating micro pores or microcracks of chromium on multi-layer nickel is an important way to reduce the total thickness of the coating and obtain a decorative system with high corrosion resistance protection. It is also the development direction of modern electroplating processes.
2. Hard chromium (wear-resistant chromium) plating has extremely high hardness and wear resistance, which can extend the service life of workpieces, such as cutting and drawing tools, pressing and casting molds of various materials, bearings, shafts, gauges, gears, etc., and can also be used to repair the dimensional tolerances of worn parts. The thickness of hard chromium plating is generally 5-50 μ m. It can also be determined according to needs, some as high as 200-800 μ M. Hard chromium plating on steel parts does not require an intermediate coating. If there are special requirements for corrosion resistance, different intermediate coatings can also be used.
3. The milky white chromium plating layer is milky white, with low glossiness, good toughness, low porosity, and soft color. Its hardness is lower than that of hard chromium and decorative chromium, but it has high corrosion resistance, so it is commonly used in measuring tools and instrument panels. To improve its hardness, a layer of hard chromium, also known as a double layer chromium coating, can be coated on the surface of the milky white coating, which combines the characteristics of both the milky white chromium coating and the hard chromium coating. It is often used for coating parts that require both wear resistance and corrosion resistance.
4. Porous chromium plating (porous chromium) utilizes the characteristics of fine cracks in the chromium layer itself. After plating hard chromium, mechanical, chemical, or electrochemical porosity treatment is carried out to further deepen and widen the crack network. The surface of the chromium layer is covered with wide grooves, which not only has the characteristics of wear-resistant chromium, but also effectively stores lubricating media, prevents non lubricated operation, and improves the friction and wear resistance of the workpiece surface. It is often used for plating the surface of Sliding friction parts under heavy pressure, such as the inner chamber of internal combustion engine cylinder barrel, piston ring, etc.
⑤ Plating black chromium black chromium coating has uniform luster, good decoration, and good extinction; The hardness is relatively high (130-350HV), and the wear resistance is 2-3 times higher than that of bright nickel under the same thickness; Its corrosion resistance is the same as ordinary chromium plating, mainly depending on the thickness of the intermediate layer. Good heat resistance, no discoloration below 300 ℃. The black chromium layer can be directly coated on the surface of iron, copper, nickel, and stainless steel. To improve corrosion resistance and decorative effect, copper, nickel, or copper tin alloy can also be used as the bottom layer, and a black chromium coating can be plated on its surface. Black chromium coating is commonly used to coat the protection and decoration of parts of aviation instruments and Optical instrument, solar energy absorption panels and daily necessities
Post time: Jul-02-2023